Cranes: Your Questions Answered
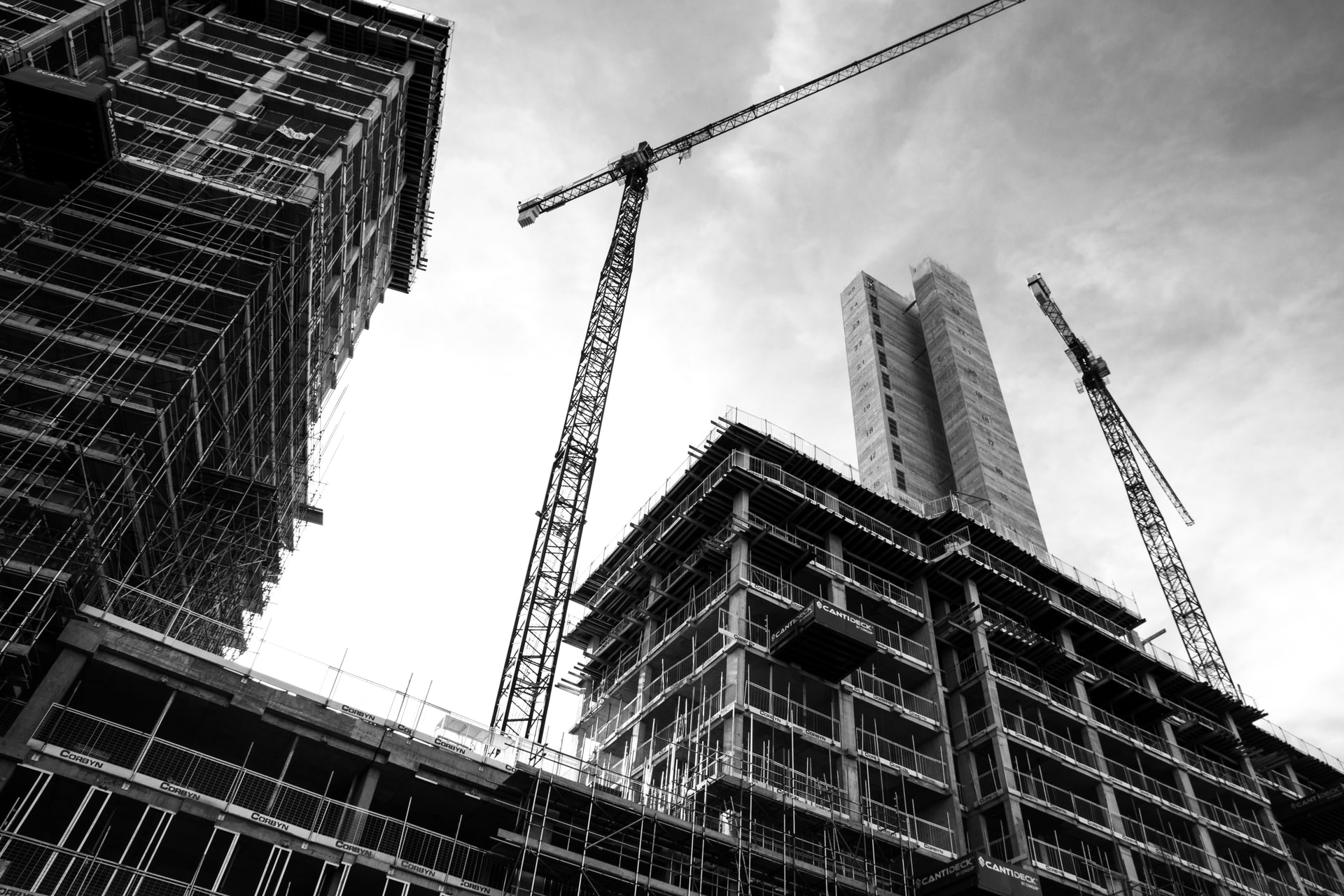
Whether you are new to the industry or you are an experienced operator looking to add new information to your arsenal, there is always room for new knowledge. With hospitality and retail industries taking a significant hit in 2020, statistics show that the shortfall could be made up by the rapid ascension of job openings in construction.
Statistics NZ said last year that according to their household labour force survey (HLFS) that construction jobs have increased by 21,000. The total number of construction workers now exceeds a quarter of a million people, a large percentage relative to the country’s population.
Plumbing and electrical services, roofing, and concreting make up the largest gains in the construction employment increase. Cranes play a large role in concreting and roofing so by nature there is going to be huge demand for hire and for purchase going forward. Everything you need to know about operation, FAQ’s, and relevant data can be found in this article.
Why Do We Use Cranes?
A crane is a machine that lifts and moves huge weights, machinery, materials, and objects for a number of applications. They’re employed in a variety of industries, including, shipbuilding, manufacturing, construction and material handling. Cranes are common along city skylines since they are required to construct the skyscrapers that we see so frequently nowadays.
Although when we think of cranes we think of tall towering structures that can be seen for as far as they eye can see, some are not so obvious. Standard truck cranes, mobile cranes, and suspended cranes are smaller versions that essentially do the same thing as tower cranes. Cranes are handy to be used not just to lift tonnes of cinder blocks hundreds of feet into the air, but to lift materials at head height where forklifts and hoists are not available.
What Causes Crane Accidents?
The United States Occupational Safety and Health Administration (OSHA) states that there are four main types of mistakes made by crane operators each year, these include contact with power lines, overturns, falls, and mechanical failure.
Dropped loads, boom collapse, rigging problems, employees being struck by the chassis as it rotates, lack of training, lack of communication, and other incidents can all rare themselves at any time. These dangers can be reduced by following safe work practises and adhering to OSHA’s crane safety requirements.
According to Safety Now:
- Human negligence is at blame for 90% of crane accidents.
- Operators breaching the crane’s operational capacity are responsible for 80% of all crane upsets.
- Swinging the boom or performing a lift without the outriggers fully extended is the cause of 54% of these occurrences.
- Electrocution results in 45 percent of all mobile crane incidents when the crane comes into touch with a power source while in operation.
- An object struck 40 percent of the victims (such as an uncontrolled hoisted load or crane part)
- In 2009, 50 percent of crane mishaps in the U.S. resulted in fatalities.
- Each year, approximately 80 lift and material handling equipment operators are killed.
How to Eliminate Crane Accidents:
- Make sure the crane is levelled and that the support surface is firm and capable of supporting the crane and its.
- Make contact with electricity utility owners to assess safeguards, such as whether lines should be disabled for safety reasons. Know where the overhead electrical lines are and be aware of them.
- Understand your crane’s capabilities and limitations, as well as any limits unique to your construction site, such as unstable soil, the presence of underground electrical lines or utilities, and high winds.
- Ensure that all other site staff are informed of the boom’s operational range and lifting actions (swing radius).
- Cordon off places within the boom’s swing radius.
- Ensure that cranes have been maintained and inspected adequately. Bear in mind that the competent person must inspect all machinery and equipment before and during each use to guarantee that it is in decent shape. If it needs to be fixed, take it out of service and don’t use it until it is!
- Determine whether materials should be stored and what machines should be placed in a safe environment.
What Are The Main Advantages of Cranes?
Advantages of using cranes vary depending on their type. However with this being said there are some obvious benefits of using cranes over other methods of lifting objects using man power. Using a crane for just a few hours can drastically reduce the amount of manpower needed for certain jobs. It is almost certainly a smarter and not harder approach to construction.
Sometimes this is not always the case. Often excavators can be used to lift objects up into the air however there are times when it becomes too dangerous. In this instance a crane is the safest measure and is the only machine capable to lift that certain weight. Most types of cranes have an unmatched level of stability which makes them the only viable solution for larger scale construction companies.
What Are The Main Disadvantages of Cranes?
To purchase and operate, cranes are highly expensive, and moving them from one location to another takes a lot of time, effort, and money. Most larger cranes come with substantial maintenance costs attributable to depreciation and repairs. They often require a considerable amount of manpower to deploy.
If you are a construction company that only needs to use a crane every now and then, hiring cranes are often a much better alternative to purchasing one. Like all heavy machinery, repair costs often pay for the machine itself over a span of years. Therefore you wont need to worry about any of that if you are prepared to pay a reasonable sum for the length of time that you will need it to get the work done.
What Are the Types Of Cranes?
Although lists online vary as to how many types of cranes there actually are, the list below from Civil Jungle details a complete itinerary of all possible types.
- Telescopic Crane
- Mobile Cranes
- Truck Mounted Crane
- Tower Crane
- Rough Terrain Crane
- Overhead Crane
- Bridge crane
- Crawler crane
- Aerial Crane
- Hydraulic Crane
- Carry Deck Crane
- Floating Crane
- Bulk-handling Crane
- Hammerhead Crane
- Stacker Crane
- Railroad Crane
- Harbor Cranes
- Level Luffing Cranes
You can learn more about the different types of crane here.
Does Weather Impede on Crane Operation?
The simple answer is yes. A general rule of thumb is that operators need to be aware of the wind direction, this is especially important for tower cranes. Even smaller winds from 0 to 20 mph need to be approached with caution. When winds exceed the 20 mph limit extreme attentiveness needs to be in place.
There is no firm and fast answer to the question. If you are an operator just make sure that you are adhering to the restrictions on the crane that you are using, these vary on height of the boom, the base that is being operated on, and the manufacturer.
In severe conditions where winds exceed 40 mph, generally all cranes have to be retracted if they are telescopic and lowered if they are tower cranes. Fog and lack of lighting possess a major threat to operators and crew below. Generally companies are pretty adept to recognising weather that may be dangerous to employees.
What Is The Largest Crane In the World?
The SGC-250, the largest crane in the world, owned by Sarens, was launched at the port of Ghent, in Belgium on 9th of November, 2018. It is known by the name ‘Big Carl’.
According to Sarens, The SGC-250’s notable features include:
- Tremendous Power. This massive crane has a maximum load moment of 250.000 metric tonnes and the ability to lift 5.000 tonnes. It’s the strongest crane of its kind, with all the features and flexibility of a fully-mobile ring crane with winches and cables, hook blocks, and the ability to slew 360°.
- Low Ground Pressure. Even at a greater radius, the SGC-250 never exceeds ground pressures of 25t/m², thanks to several wheel bogies on double ring beams and spreader mats.
- Impressive Flexibility. The crane’s main boom can be extended from 118m to 160m, and the jib can be extended up to 100m. This combination provides an incredible height of about 250m, or an equally astonishing radius of 275m. This flexibility guarantees that whatever combination clients need, we can build it: all on a double-ring design with an outer diameter of no more than 48,5m.
- Extensive Coverage. The crane can operate on two hook blocks: one on the main boom and one on the jib. This allows it to cover each area of the job site while maintaining a combination of strong capacities and fast operations.
- Exceptional Safety Standards. Sarens has invested tremendous effort in the crane’s safety and continuity. This reflects in the highest performance level (PL E) and full redundancy system on the hoisting and slewing system, achieved by intelligently connecting and steering all 12 engines with six power packs.

According to Heavy Lift News, this was the first in a series of more than 700 lifts that the SGC-250 will perform here over the next four years, on behalf of client Bylor and project owner EDF/ NNB. The loads will range from precast concrete elements to pipe sections, steel rings, and machinery equipment weighing from 10 to 1.600 tonnes. The SGC-250 will also lift five major parts of each unit’s steel containment liner and dome.
Big Carl was designed in-house by Sarens, a Belgium-based crane rental service. The crane was shipped from Ghent, Belgium to the Hinkley Point C project location in Somerset, UK on over 250 trucks over a period of months, according to Sky News.
Lifting huge large loads is only possible because of the SGC-250’s height – 0.25 km high in its tallest configuration, a little taller than One Canada Square in London’s Canary Wharf – and sheer load capacity. Such immense lifting height is the product of a 118-metre high-strength steel built main boom, which stands 160 metres high, and a 52.3 metre heavy duty jib which adds an additional 100 metres.
Why ‘Big Carl’? That’s in honour of Sarens director of technical solutions, Carl Sarens.
The design process involved 16,000 hours of R&D, 6,000 hours of CAD design and more than 25,000 hours of specialist design detail work. Construction commenced in August 2017, using components sourced from across Europe, and was completed in 14 months ready for the official public launch in November 2018.
Conceptually, the SGC-250 was inspired by the trend towards modularisation within construction. Increasingly, large portions are being prefabricated within a controlled environment, then transported to construction sites for lifting into their final positions. These individual models are so heavy, cranes with very high lifting capacities are required – and tall lifting heights are needed to deal with the size of major projects such as Hinckley Point C.
After construction in Belgium, Big Carl was transported to the UK in 2019, with 280 trucks taking it piece-by-piece for reconstruction on site – which required the use of five smaller cranes. After 10 weeks, the SGC-250 was boomed up in August and began its first lift in mid-September, with the first significant lifts to begin in spring 2020. It is scheduled to work on the site for four years in a £20 million contract, supported by 52 other tower cranes.
Cleverly, the crane was transported in boxes that are now being used as its counterweights. These were filled with locally sourced material on site: there are a total of 52 counterweights, each weighing 100 tonnes.
There is 6km of rail track at the site, allowing the crane to travel between three lifting locations – an industry first for a fully-rigged crane, says Sarens. Smaller models such as the SGC-120 rest on a steel ring, but due to the scale of the building operation, the SGC-250 moves on high-grade steel rails that allow it to shift between positions without the need for reassembly.
It runs on 96 individual wheels when moving between positions. But despite its tremendous weight, careful design of the four bogies that run on a double ring beam made from high-strength steel and a spreader mat means it exerts a maximum ground pressure of just 25 tonnes per square metre. It can also slew 360 degrees, thanks to an extra 128 wheels. The ring itself has a diameter of less than 50 metres.
For the actual lifting, there are more than two kilometres of thick steel cables to which the crane’s hook is attached. Similar cables are also are used to operate the pulleys that lift the boom, and these must take the enormous strain of moving the massive components.
What Is the Strongest Crane In the World?
The Taisun Crane is currently the strongest crane in the world. It has the record for the heaviest lift of any crane maxing out at 20,133 metric tonnes. The crane is used to construct oil rigs and is able to maneuver and sub ships out onto the water. The crane is located in Yantai, China and spans larger than a soccer field.
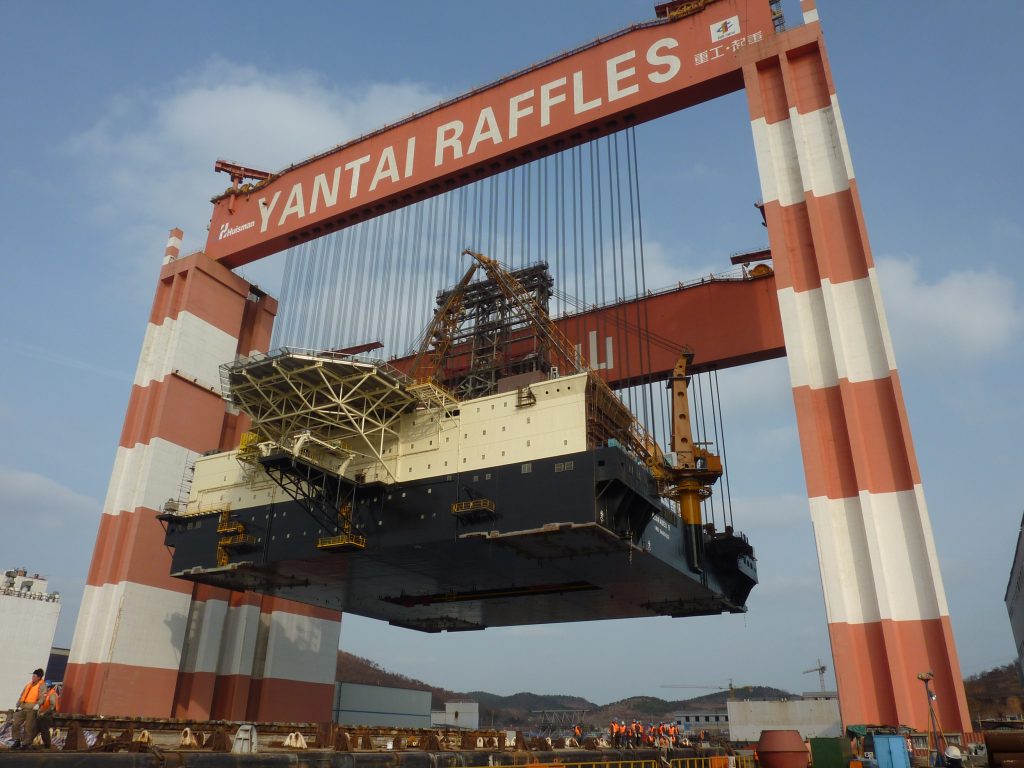
Holding the record for the top 3 heaviest lifts; the Taisun crane in China is the strongest crane that exists in the world today, according to Pacific Industrial. With a working load limit of over 44 million pounds or 20,000 metric tons this crane is surely a modern marvel.
The amount of wire rope required to operate Taisun is nearly 50,000 meters or just over 31 miles; allowing it to lift a maximum of 80 meters. While not everyone may need 31 miles of wire rope, or have a need to lift 44 million pounds, we have a wide variety of materials required to lift, push, pull, and move whatever is in your way.
https://cranepedia.com/gantry-crane/yantai-raffles-taisun-taishan-world-record-crane-20000-ton-lifting-capacity/Cranepedia states that, it completed its first commercial lift of a deck box lifting and installation of COSL Pioneer, also the first drilling semi-submersible built in China in 2008.
It has achieved its name for world’s heaviest topsides crane lift during the deck box lifting and installation of Saipem Scarabeo 9 in 2009
Achievement of numerous awards including Spotlight on New Technology Award and Woelfel Best Mechanical Engineering Achievement Award from American Society of Mechanical Engineers, both during Offshore Technology Conference 2008.
Ongoing Innovations
At the other end of the size scale, one example of continued innovation in the crane industry is the new TIDD PC28, manufactured by TRT in Australia and New Zealand. This is the safest pick and carry crane in its class, featuring Slew Safe® and unrivalled quality and workmanship. This crane is manufactured in-house by the team at TRT from its Cranes Brisbane headquarters.
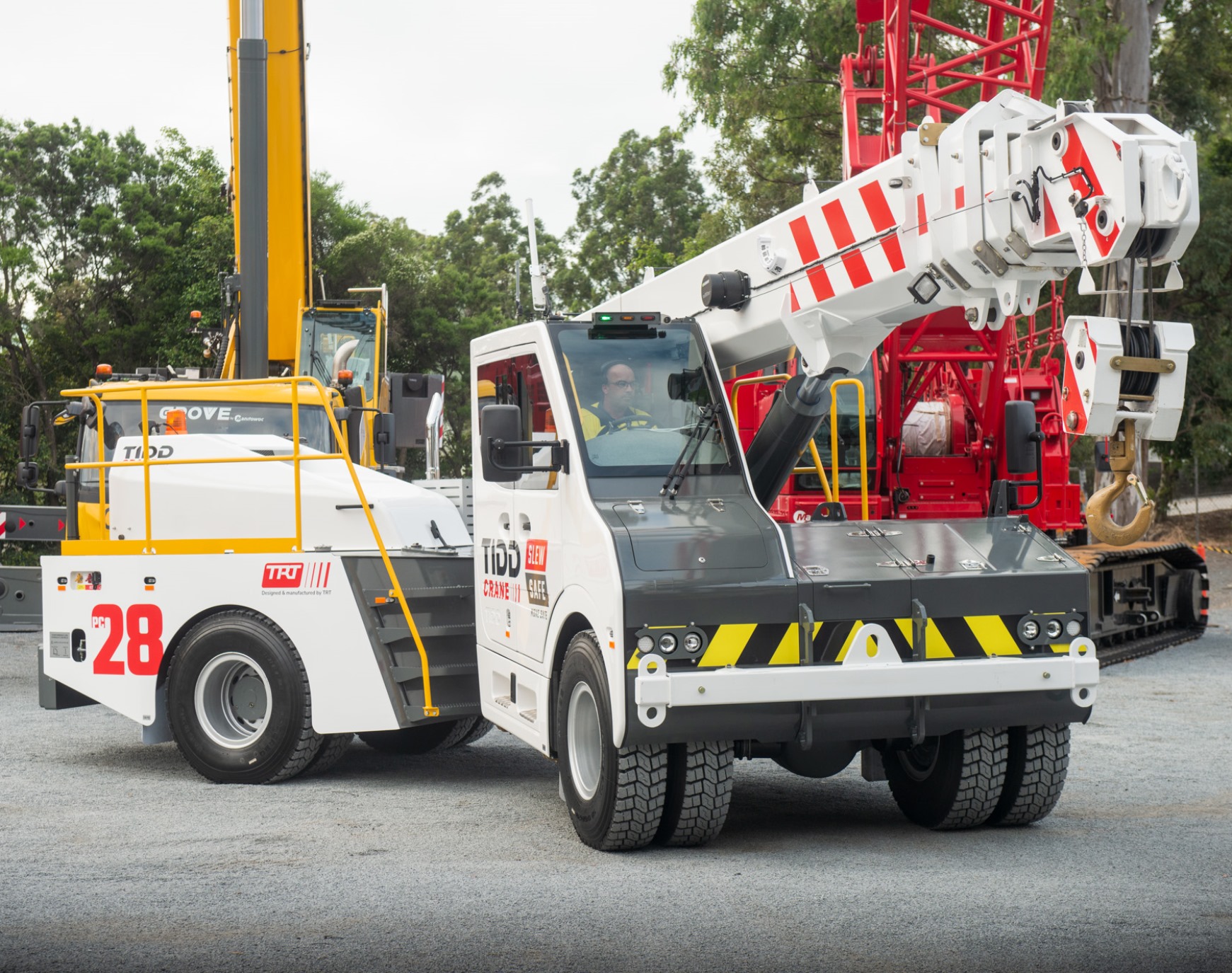
With a huge 28t lift capacity, the TIDD PC28 has been designed and manufactured by TRT with a focus on safety and operator comfort:
- Full power, 4 section telescopic boom
- Slewing up to 44° for max manoeuvrability onsite
- Small footprint to move and set up in tight spaces
- 75% stationery chart and 66% pick and carry chart
- Ability to road its own 2.3t counterweight
- ROPS certified cabin for maximum driver safety
- Slew Safe for maximum operation safety is recommended
- New optional 1.1t Superlift Counterweight available
Full Power Boom
With the new 6.12-18.64m full power boom, a 75% stationary chart for the heavy lifts and 66% pick and carry chart, the Tidd PC28 packs a massive punch.

The high tensile steel, full power boom telescope Sections 1 and 2 are fully synchronised and provide hook compensation. The telescopic section 3 is independently operated with its own hydraulic cylinder.
The TIDD PC28 delivers outstanding lifting capacities for improved efficiency and greater lift options, setting a new benchmark for the industry.
- 28t on the fixed lug
- 27.6t on the running rope
- 25t pick and carry on the 2nd lug
Focus on Safety
The TIDD PC28 is designed to provide outstanding performance while providing better operator safety both on the road and on the job site than seen in this class of crane. The safety features have been designed to maximise safety in consultation with industry! Safety features include:
- Robway LMI System
- Dynamic LMI with a deadlock switch inside the cabin and LMI bridging switch outside the cabin.
- ROPS (Rollover protection system) Cabin
- Air suspension seats for reduced operator fatigue
- 3 point integrated safety belts
- ABS braking system
- Improved visibility with wide view top glass and optimised mirror placement
- Slew Safe is recommended to optimise safety
Dynamic Load Indicator
This serious safety feature is exclusive to TRT’s TIDD Crane which allows safer operation on uneven job site surfaces than any other crane in its class!
- Robway RCI8510 Dynamic Load Indicator with automatic cutouts and digital display.
- A dash-mounted deadlock switch allowing a temporary increase to 110% RC only with reduced function speeds.
- A key locked Bridging switch is mounted externally on the cab limiting access to authorised persons only.
About TRT Australia
For more than 50 yrs TRT have focussed on innovative and customised solutions, design excellence, product development and sourcing. Their key areas of focus include crane sales, crane manufacturing, design and engineering, crane service and repair including major inspections and rebuilds, crane parts, trailer manufacturing, and heavy transport and equipment design and manufacture.