How to Identify and Mitigate Crane Structural Failures in Australia
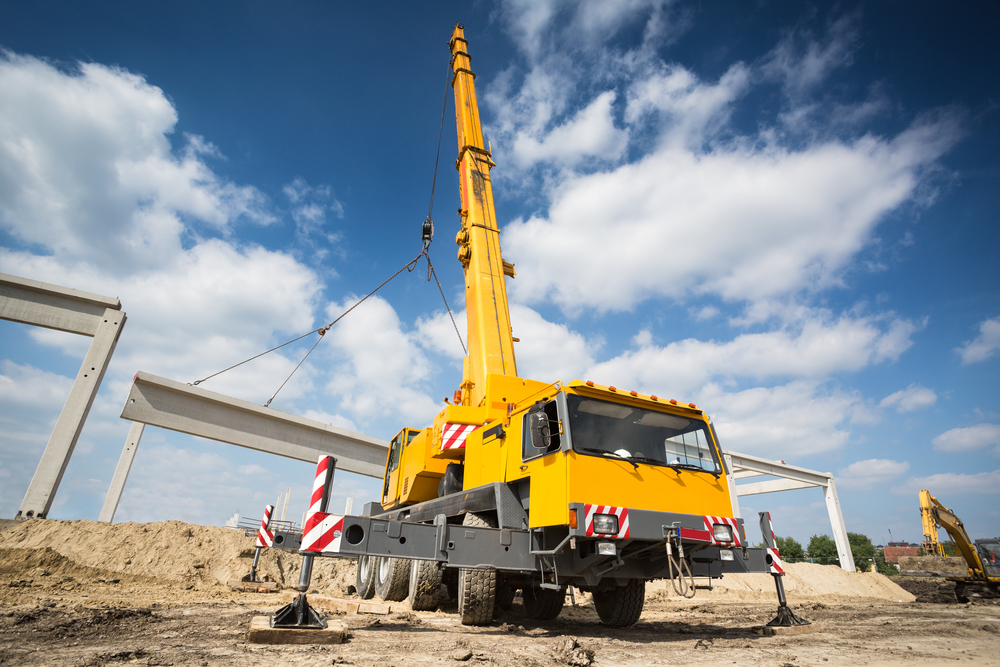
Cranes are an integral part of Australia’s construction, mining, and industrial sectors, playing a crucial role in lifting and transporting heavy materials across worksites. These machines are indispensable in large-scale infrastructure projects, high-rise construction, port operations, and resource extraction sites, where efficiency and safety are paramount. However, the reliance on cranes also brings significant risks, particularly when it comes to crane structural failures.
A crane structural failure can result in catastrophic consequences, including equipment damage, costly project delays, and, most critically, serious injuries or fatalities. In Australia, where stringent workplace health and safety regulations govern crane operations, ensuring structural integrity is not only a matter of compliance but a fundamental responsibility for operators, engineers, and employers.
Regular crane inspections, preventative maintenance, and adherence to Australian safety standards are essential in mitigating structural risks and maintaining operational efficiency. Understanding the causes, warning signs, and preventative measures can help organisations avoid structural failures and enhance overall workplace safety.
Understanding Crane Structural Failures
What Is a Crane Structural Failure?
A crane structural failure occurs when a crane’s key load-bearing components, such as the boom, jib, tower, or base, experience damage or degradation, leading to compromised stability and performance.
This failure can stem from material fatigue, overloading, poor maintenance, or environmental factors that weaken the crane’s structural integrity. The consequences of such failures can be severe, including sudden collapses, loss of load control, and irreparable damage to the crane itself.
In Australia, numerous incidents have highlighted the dangers of crane structural failures. One notable example is the collapse of a tower crane in Sydney, where structural fatigue and inadequate maintenance contributed to a dangerous failure, resulting in worksite evacuations and significant project delays.
Similarly, mobile crane failures in mining operations, particularly in Western Australia, have been linked to corrosion, wear, and improper loading practices, underscoring the need for rigorous crane inspection protocols. These incidents reinforce the importance of identifying failure risks before they lead to catastrophic outcomes.
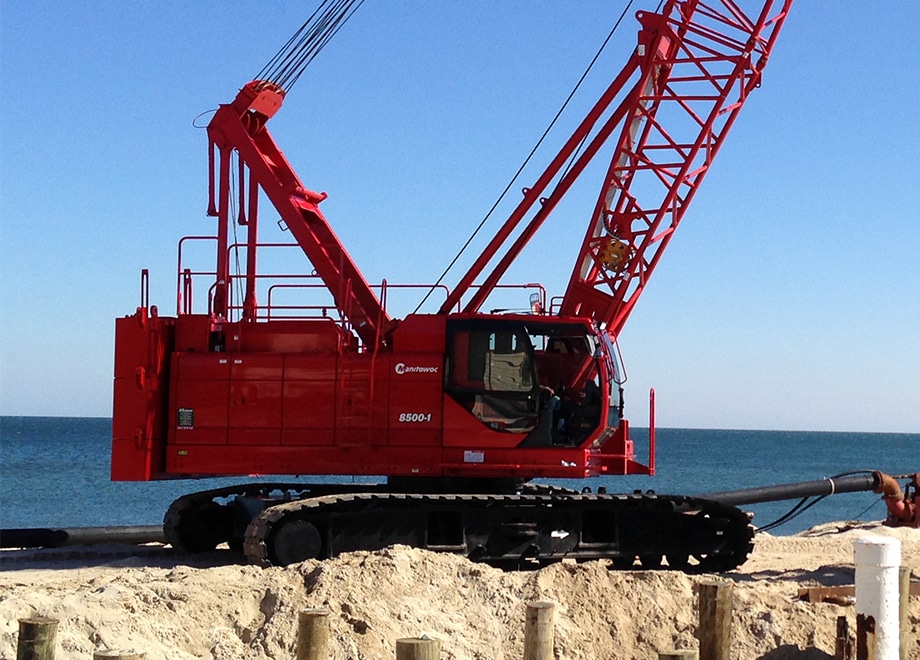
Common Causes of Crane Structural Failures
Material Fatigue and Wear
Cranes endure substantial stress over their lifespan, with repeated lifting, lowering, and swinging of heavy loads placing immense pressure on structural components. Over time, metal fatigue develops, causing microscopic cracks that can grow and eventually lead to structural failure. This gradual deterioration is particularly concerning in older cranes that have undergone extensive operation without adequate crane inspections and maintenance.
Overloading and Improper Use
Exceeding a crane’s designated load capacity is a major contributor to structural failures. Overloading places excessive strain on the crane’s boom, cables, and foundation, leading to bending, warping, or outright collapse. Improper use, such as swinging loads too abruptly or extending the boom beyond safe angles, further exacerbates the risk.
In Australia, strict regulations govern load testing and safe crane operation, yet failures still occur when operators ignore capacity limits or use the crane in conditions beyond its design specifications.
Corrosion and Environmental Exposure
Australia’s diverse climate, ranging from coastal environments to extreme mining conditions, significantly impacts crane longevity. Cranes operating in coastal areas, such as Sydney, Brisbane, and Perth, are particularly vulnerable to saltwater corrosion, which weakens structural components over time.
Likewise, cranes in mining operations face exposure to dust, moisture, and chemicals, accelerating rust and metal degradation. Without proper protective coatings, regular inspections, and proactive maintenance, corrosion can lead to unexpected crane structural failures.
Inadequate Maintenance and Inspections
Routine crane inspections and preventative maintenance are essential in identifying potential issues before they escalate into structural failures. Neglecting routine maintenance can allow minor defects to worsen, increasing the risk of sudden breakdowns. In Australia, failure to comply with AS 2550 and AS 1418 crane inspection standards can result in severe penalties, worksite shutdowns, and liability in the event of an accident.
Faulty Manufacturing or Installation Defects
Poor design, low-quality materials, and improper assembly can all contribute to premature crane structural failures. Defective welding, misalignment of load-bearing parts, and substandard components create weak points that may fail under stress. In Australia, all cranes must meet rigorous engineering and manufacturing standards, but issues still arise when inferior components are used or installation errors go unnoticed.
How to Identify Crane Structural Failures in Australia
Visible Cracks and Deformations
Inspecting load-bearing components for cracks, dents, or warping is crucial in identifying early signs of structural failure. Even minor deformations can indicate underlying stress that may lead to a breakdown under load.
Unusual Noises or Vibrations
Excessive vibrations or strange noises, such as creaking or grinding, often signal internal issues within a crane’s structure. These symptoms may indicate metal fatigue, joint misalignment, or excessive wear.
Misalignment or Shifting of Crane Components
Misalignment of booms, towers, or support structures can compromise stability. If a crane appears to be leaning or shifting unexpectedly, an immediate crane inspection is necessary.
Signs of Corrosion, Rust, or Metal Fatigue
Rust patches, flaking paint, or weakened metal surfaces can signal corrosion-related structural deterioration. Cranes exposed to Australia’s coastal air, industrial pollutants, or mining dust require frequent checks for such issues.
The Role of Routine Crane Inspections
Australian Crane Inspection Standards (AS 2550 and AS 1418)
Compliance with AS 2550 and AS 1418 standards ensures that all cranes undergo regular inspections and maintenance to prevent structural failures. These standards outline requirements for daily, periodic, and annual inspections, helping to identify potential defects before they lead to catastrophic failures.
Daily, Weekly, and Annual Inspection Checklists
- Daily checks: Operator-led inspections for visible damage, misalignment, and load-bearing stability.
- Weekly checks: More thorough assessments of mechanical integrity and lubrication.
- Annual inspections: Certified crane inspectors in Australia conduct detailed structural integrity assessments and load testing.
How to Mitigate Crane Structural Failures
Preventative Maintenance Strategies
- Implement regular maintenance schedules to keep cranes in optimal condition.
- Use non-destructive testing (NDT) techniques to detect internal flaws before they become critical.
- Ensure proper lubrication, bolt tightening, and component replacements to extend crane lifespan.
Training and Compliance for Crane Operators
- Conduct structural failure recognition training for all crane operators.
- Adhere to Safe Work Australia regulations governing crane safety.
- Ensure engineers and inspectors perform comprehensive load testing and stress analysis.
Emergency Response in Case of Structural Failure
- Cease crane operations immediately if structural issues are detected.
- Implement safety protocols to prevent injuries and contain damage.
- Report failures to regulatory bodies as required under Australian workplace safety laws.
The Future of Crane Safety in Australia
Advancements in sensor technology, AI-based predictive maintenance, and remote monitoring systems are transforming crane inspections and failure prevention. Automated diagnostic tools can now detect material fatigue and structural weaknesses long before visible damage occurs, improving safety and efficiency.
Final Thoughts
Preventing crane structural failures in Australia requires rigorous inspections, preventative maintenance, operator training, and regulatory compliance. By identifying warning signs early and following best practices for crane maintenance, businesses can ensure workplace safety, equipment longevity, and operational efficiency. Prioritising proactive crane care is not just a legal requirement—it is an investment in a safer, more reliable work environment.