A Guide to Maintaining Your Heavy Equipment
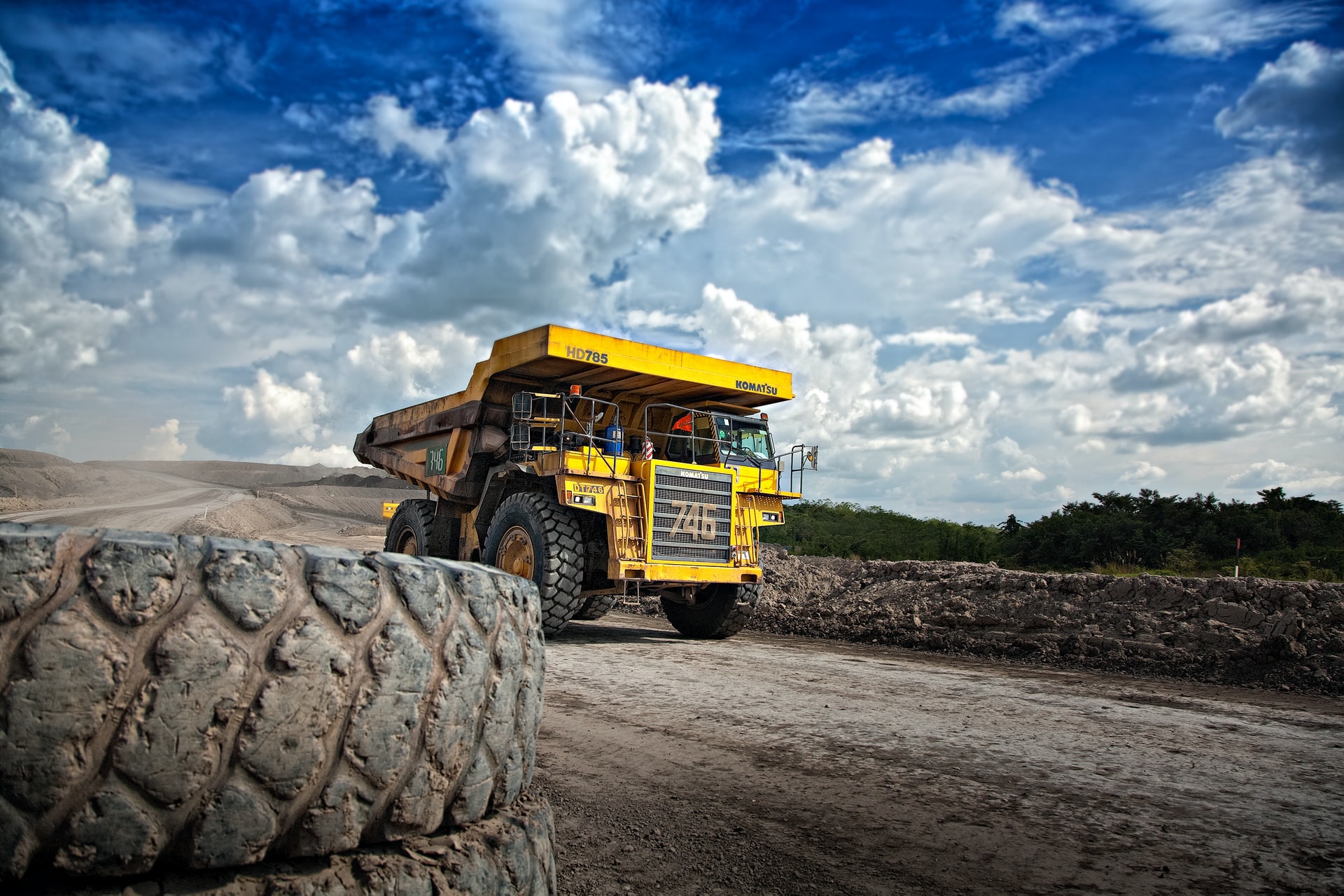
When operating heavy machinery, there are always going to be downfalls for using such large equipment in often dusty and less than perfect working areas. Keeping on top of general wear and tear of equipment can and will ensure the longevity of expensive equipment and will prevent the costly time out in days to come. Many site operators fail to realise that the cost of breakdowns is not just the cost and labour of extra parts, it is also at the expense of the ground lost while the machine is out of operation. Lost days mean possible slippage of schedules with its attendant problems.
Rather than time spent on the sidelines, as a site manager, you are much better positioned than competitors if you have a maintenance plan set up and ready to go. Ensure that employees are on board and are following the procedures you have laid out. A study by Caterpillar found that each machine has an average idle time of 400-800 hours per year, The result of this was a $2000-4500 loss each year costing most construction companies more than they care to realise.
Below are five tips for establishing and managing a heavy equipment maintenance program. These tips apply to job sites both small and large. Small but regular checkups will keep your machinery and employees active for longer periods.
Start Each Shift With Checklists and End Of Day Protocols In Place
It is always a good idea to have daily, weekly and monthly checklists at the beginning of each shift to inspect each piece of equipment for problems or items needing servicing. Time set aside to take care of issues is more important than most operators realise. These checklists should include any required cleaning, safety items, lubricants and operating parts.
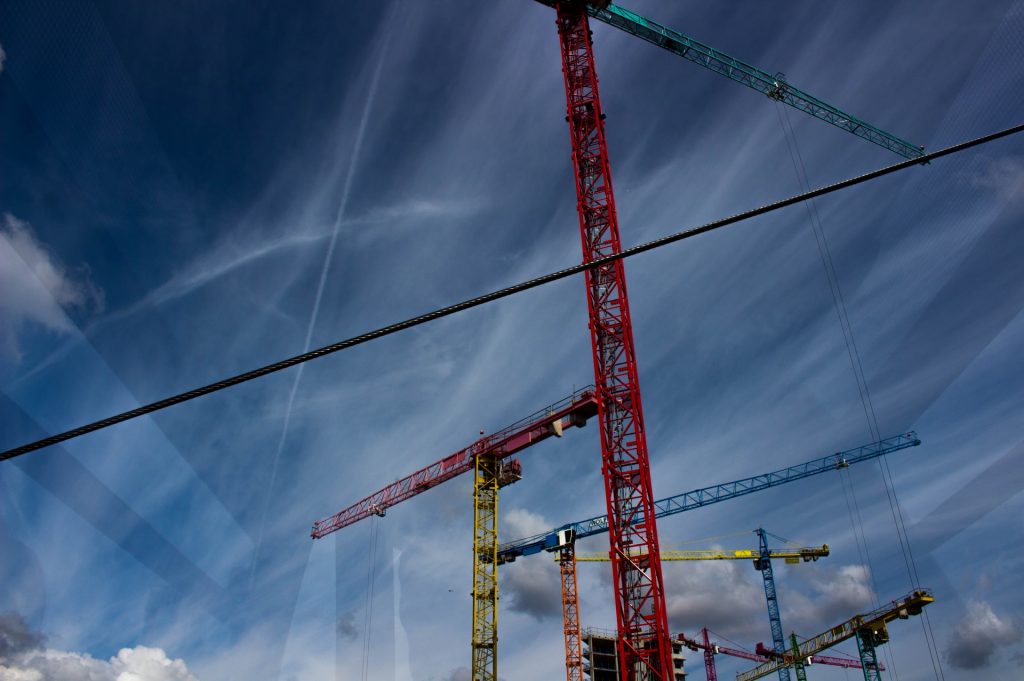
Shielding heavy equipment from the elements is also a large part of keeping machinery running, this is even more applicable in the colder months when the risk of seizing parts becomes more apparent. Greases and lubricants wash and evaporate after rainfall so it is important to consider where you put your machinery to sit. Even if a machine is partially covered, it is still better than leaving a full machine exposed.
End of day cleaning and checking of wearing parts is important. This will often dictate when maintenance is carried out. Oftentimes it is better to replace components before they break which could cause catastrophe, wrecking other parts in their wake. This is not to mention the potential harm of employees if something violently sheers.
Training Of Operators and Communication With Maintenance Teams
Ensuring all operators and support personnel are well trained is crucial to the efficient operation of any worksite. They should know and understand the equipment and be aware of maintenance requirements. In an ideal scenario, operators should be in ready contact with maintenance personnel to ensure that both are on the same page when it comes to what parts are under more strain than others. Some breakages are unavoidable but with a thorough understanding amongst employees of what is and what isn’t likely to break, most of the unknown are eliminated.
Most inspectors require standards by law, but it is also a good idea to set up your checklists. Often regulation requirements are the bare minimum and only put in place to ensure workplace safety. Seldom do these checks bear in mind the good health of the machinery. Excavator’s, Cranes, and Trucks all have weak points, most experienced operators are aware of these and when to service them.
Use Machinery Within its Limitations
To reduce components and machine failures, operators should observe published performance limits for their equipment. Furthermore, clear operating procedures should be established from the beginning and operators should be trained to follow recommended practices.
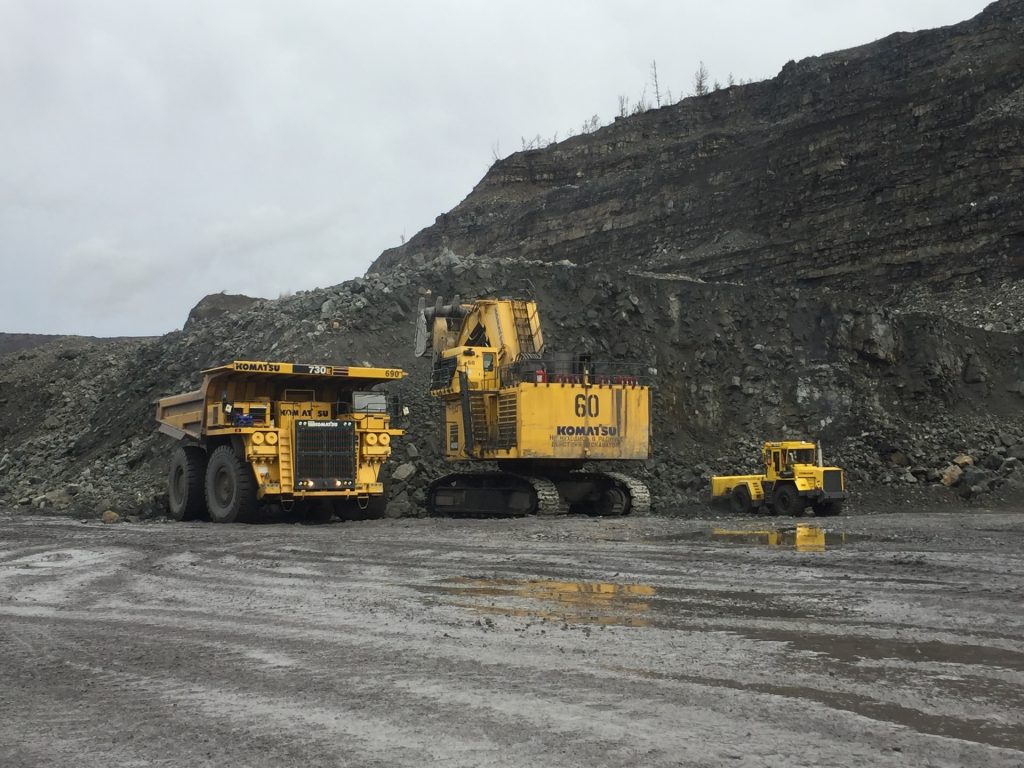
Loads, torque limits, speeds, feeds and more should be carefully monitored and controlled by machine operators. Excessive wear, tear and stresses on operating parts can dramatically shorten the life of equipment or create a sudden (and often dangerous) equipment failure. Different manufacturers often have different load weights so be on the lookout when employees work from machine to machine daily.
Establish a Backup Repair Team
For large or long-term projects, it may be cost-effective to establish and maintain a rapid response repair team. Depending on circumstances, this team would be available on call with commonly used spare parts (such as filters, fluids and belts) and have access to a heavy lift service truck. Forklifts are also important but are not necessary. Think of this as roadside assistance but for construction equipment.
Data from preventative maintenance repair records can be used to plan and design this effort and to identify specific critical parts. Coordination with spare parts suppliers to maintain an onsite inventory of critical spare parts can often ensure that there is no lack of common parts that may be required at any time. Occasionally rare parts can fail, but the idea of this team is to cover the most common and frequent mishaps that happen with equipment.
Implement a Preventative Maintenance Program
Reactive maintenance (fixing equipment when it breaks) is much more costly than planned maintenance. The industry rule of thumb is that reactive maintenance costs two to five times more than planned maintenance.
A great way to keep an eye on big, expensive equipment is by developing and maintaining a preventative maintenance program. The idea of this is to have backups of equipment before it breaks. A preventative maintenance program often goes hand in hand with the backup repair team.
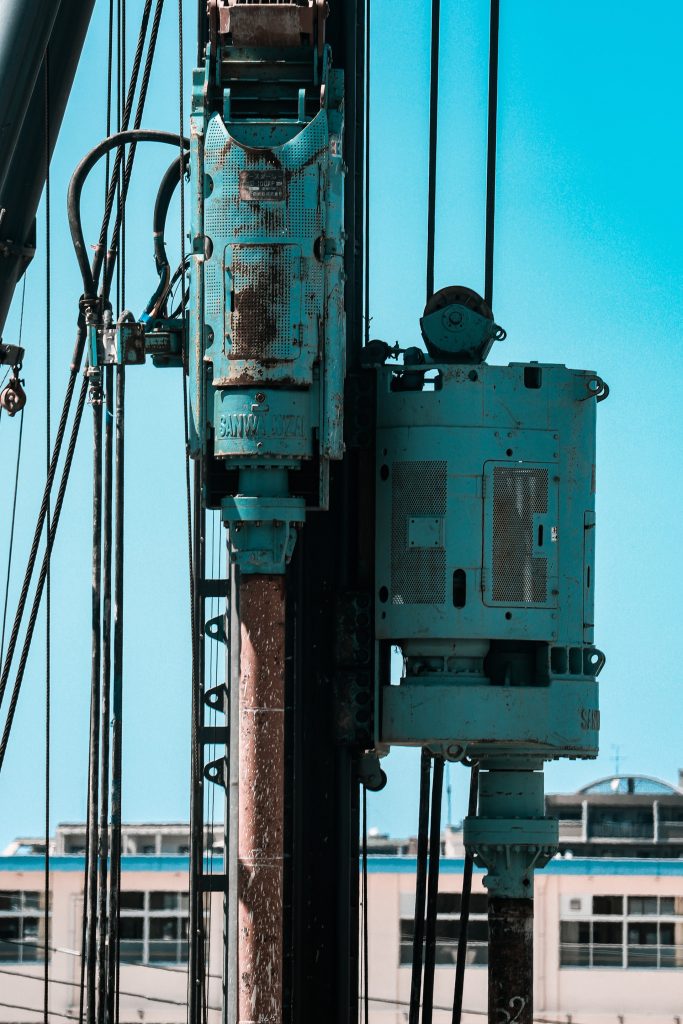
The initial program can be based on equipment manufacturers’ operating manuals and standard repair procedures for preventative maintenance scheduling. Then, as records accumulate over time, improved maintenance procedures can be incorporated into the system from actual equipment parts failures and repair data. Again, computerized maintenance management software provides the core system support for starting and maintaining a project management program.
Investment in heavy machinery is expensive, and it pays to ensure that equipment is up and running when it’s needed. While direct equipment costs are easy to identify, costs of breakdowns, idle equipment, or operator error are hidden and difficult to nail down. Ensuring that all equipment is well serviced and looked after can vastly reduce the costs of operation if done correctly.
You can read the original full article here