Key Differences Between New and Used Crane Inspections
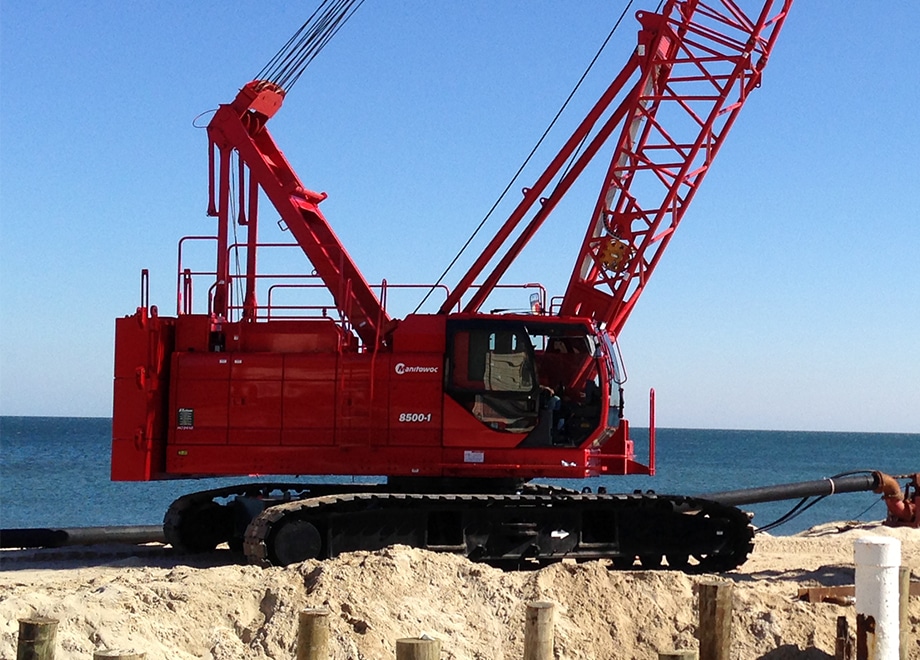
Crane inspections are crucial for ensuring safety and operational efficiency in any workplace. Whether you’re dealing with a brand-new crane or a pre-owned one, inspections help mitigate risks, comply with Australian safety standards, and optimise performance.
However, the inspection process for new cranes is vastly different from that for used ones. While new cranes focus on verifying compliance with manufacturing specifications and installation quality, used cranes require detailed assessments to identify wear, damage, and overall suitability.
This article explores these key differences, providing valuable insights to help crane owners and operators in Australia maintain safety and compliance.
Inspection Goals: New vs Used Cranes
New Cranes
When inspecting new cranes, the primary focus is on confirming compliance with manufacturer standards and ensuring proper installation. These inspections are critical to validate that the crane meets the required safety and operational benchmarks.
Inspectors also verify that all components are correctly assembled and calibrated according to the manufacturer’s guidelines. Additionally, load testing and certification documents must be reviewed to confirm the crane’s ability to handle specified loads safely.
Used Cranes
Inspections for used cranes have a different emphasis. The primary goal is to evaluate the crane’s condition, including wear and tear on critical components. Inspectors look for any signs of damage, poor maintenance, or improper repairs that may compromise safety.
Furthermore, the crane’s suitability for continued use under specific site conditions must be assessed, ensuring it remains a reliable and safe piece of equipment.
Documentation Requirements
New Cranes
For new cranes, documentation plays a vital role in the inspection process. The checklist typically includes factory test certifications, installation records, and warranty details.
These documents confirm that the crane has been manufactured and installed to meet Australian safety standards, such as AS 2550 and AS 1418. Ensuring that this paperwork is complete and accurate helps prevent delays in project timelines and ensures compliance with regulatory requirements.
Used Cranes
In contrast, used crane inspections involve a thorough review of existing maintenance logs and previous inspection reports. Inspectors also check the crane’s repair history to identify any recurring issues or inadequate fixes. Additionally, verifying re-certifications is essential to confirm that the crane continues to meet Australian safety standards after repairs or modifications.
Common Inspection Areas and Differences
Structural Components
New crane inspections focus on verifying that all structural components are correctly aligned and free from manufacturing defects. For used cranes, however, the inspection centres on identifying cracks, corrosion, or fatigue that may compromise the structural integrity.
Mechanical Systems
For new cranes, mechanical systems are checked to ensure that all moving parts operate smoothly and as per the manufacturer’s specifications. In used cranes, inspectors prioritise identifying signs of excessive wear, rust, or outdated systems that may require immediate attention or replacement.
Electrical Systems
New crane inspections ensure that electrical wiring, control panels, and software systems are correctly installed and functional. In used cranes, inspectors look for faults in wiring, outdated technology, or evidence of improper repairs that could pose a safety hazard.
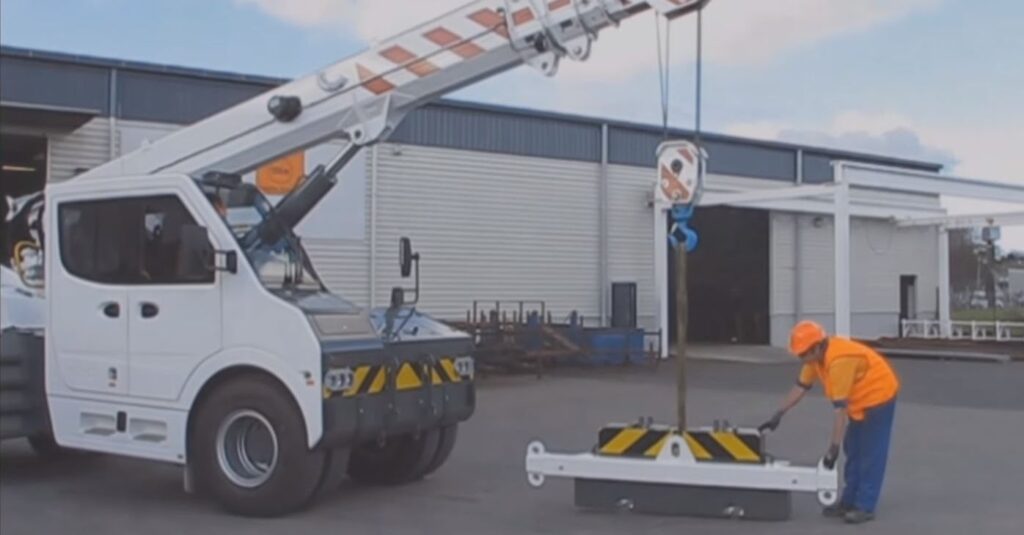
Special Considerations for Used Cranes
Used cranes require more extensive assessments to ensure safety and reliability. Engaging a third-party inspection service before purchasing a used crane is essential to identify potential issues.
Non-destructive testing (NDT) techniques, such as ultrasonic or magnetic particle testing, can uncover hidden damage that is not visible during a standard inspection. Additionally, operators should evaluate whether the crane needs refurbishment or has reached the end of its operational life, necessitating decommissioning.
Frequency of Inspections
New cranes require an initial inspection immediately after installation to ensure they meet all safety and compliance standards before being put into operation. On the other hand, used cranes must be inspected more frequently and in greater detail due to their history of use and higher risk of component failure. Regular inspections for used cranes help identify potential problems early, reducing the likelihood of costly breakdowns or accidents.
Cost Implications
New Cranes
While new cranes generally have lower inspection costs initially, their higher upfront purchase price can be a significant investment. However, these costs are offset by the reduced likelihood of repairs or failures in the early stages of operation.
Used Cranes
Used cranes typically have a lower upfront cost but require more frequent and detailed inspections, which can increase operational expenses. Potential repair and refurbishment costs must also be factored into the overall investment, making a thorough pre-purchase inspection critical to avoiding unexpected expenses.
Case Studies/Examples
Consider a new crane that passed its initial inspection but was found to have a minor manufacturing defect. Early detection through the inspection process allowed the defect to be rectified without impacting operations. In contrast, a used crane purchased without a thorough inspection later suffered a critical mechanical failure, resulting in costly downtime and repairs. These examples highlight the importance of tailored inspection processes for both new and used cranes.
Final Thoughts
The inspection needs of new and used cranes differ significantly, with each requiring a tailored approach to ensure safety, compliance, and efficiency. While new crane inspections focus on verifying compliance with manufacturer standards, used crane inspections are centred on assessing wear, damage, and ongoing suitability.
By understanding these differences, Australian crane owners and operators can minimise risks, reduce downtime, and maintain compliance with safety standards. Always engage a certified inspector to ensure your crane is fit for purpose and ready to perform reliably on your worksite.