Purpose Built Crane Trailers Set To Make Haulage Easier
Australian and New Zealand company TRT has met the challenge of transporting and lifting heavy equipment head on with specialised equipment to suit individual needs of clientele. The customised trailers are all purpose built to suit the transporting of cranes, counterweights and other crane components.
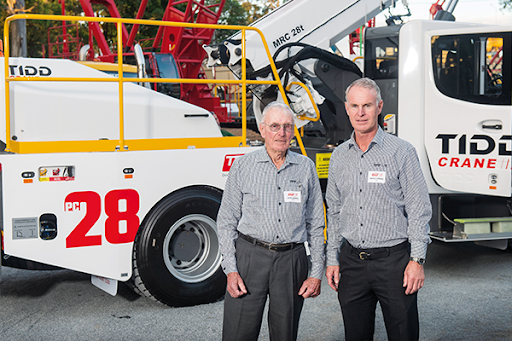
Australian and New Zealand company TRT has met the challenge of transporting and lifting heavy equipment head on with specialised equipment to suit individual needs of clientele. The customised trailers are all purpose built to suit the transporting of cranes, counterweights and other crane components.
No matter the crane make or model, TRT has a semi-trailer, B-double, skeletal or road train solution to suit. TRT has designed these specialist crane trailers to be light weight allowing the operator to optimise the payload per axle, and now with VersaLock, their newly patented and highly innovative load restraint mount system, the operator can be confident the payload is positioned on the trailer so that it is legal on the road, no matter the set up or where the crane is going.
TRT has been developing and manufacturing trailers since the early 70s. Cranes and Lifting recently spoke to Bruce Carden, manufacturing director, to discuss recent developments to the product line up.
“Predominantly, our business looks at building trailers for oversized items and to do that, the trailer itself is reconfigured as a low loader or low decker. In more recent years, we’ve extended our range and we now build a range called crane support trailers. This range is designed to carry a range of ancillary equipment a crane needs when it’s deployed. This can include counter weights, the crane base plate, the outrigger pads to spread the load of the outriggers when the crane is set up, it could be the hook block or the de-rigging box.”
Bruce Carden, Manufacturing Director
TRT purpose build crane trailers to carry crane related items in specific locations on the trailers, and trailers deployed in a specific order to site for a number of reasons.
“When a crane operator gets to site with all of their gear, they need to configure and mobilise the crane and get it to the point where it can conduct its first lift. With a standard trailer, this process can take hours depending on the size of the crane,” said Carden.
“If the operator can get to site and have the gear turn up in the right order on the trailers, that’s the first step. From their customer’s point of view, they are hiring the crane for the job and he can see the operator has a system, that it’s a quick and efficient system and, because it’s all configured properly, its saving time. And from the customer’s point of view, they believe they are getting value for money,” said Carden.
“As you can appreciate, large cranes have a very high hourly rate and if the crane can be configured efficiently this will significantly reduce cost in a job or improve competitiveness during a tender or quote process, that’s a real and tangible return on investment,” he said.
According to Carden, there are a number of issues relating to safely securing loads of various shapes and sizes to the tailer.
“When you put counterweights on to the steel deck of a trailer and you don’t put rubber between the counterweight and the deck, you get steel on steel, which is very slippery. These counterweights weigh between 10t and 15t, so if the driver brakes suddenly, the counterweights can become missiles. And when you consider that 9 times out of 10 they are not tied down correctly when chains and dogs are used, the safety risk is extreme,” he said.
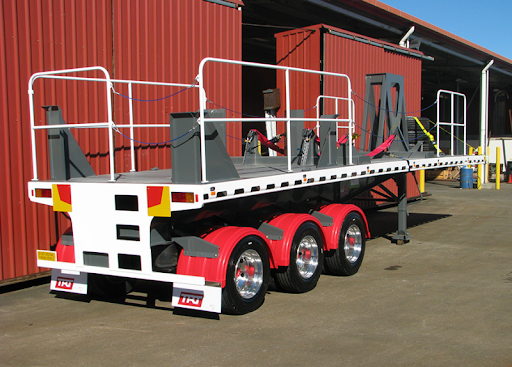
Another issue relates to the correct positioning of weights on the trailer, says Carden.
“If the load isn’t positioned correctly you won’t get all the axles to weigh correctly. Our purpose-built trailers are engineered with specific load restraints in exactly the right place, so all the axles weigh correctly, significantly reducing risk because no chains and dogs are required. So from a duty of care perspective, as the owner of the crane business, you are confident that when the trailers are deployed, the next phone call isn’t going to be from a problem, or worse, an accident,” he said.
TRT has been building crane counterweight support trailers for more than eight years and over this period several clients have recognised the various benefits.
“Over the years, we’ve worked closely with a number of clients. Borger Cranes, for example, has around 45 of our purpose-built crane trailers. They are realising genuine benefits in terms of safety and the deployment of counterweights on site,” said Carden.
Carden explains the benefits of a system designed to make TRT crane trailers even more flexible.
“In the past, trailers were designed and manufactured for a particular crane, and what I call the ‘furniture’, the various pieces of equipment that travels with the crane, have been attached to the trailer at various fixed points or positions.
“More recently, we developed quite a unique attachment point called the Versa-Lock and we are very excited about it, we’ve just been awarded an innovation patent. It was on display at the recent CICA Conference and it caused a lot of interest. VersaLock is a bolt on device which can be moved up and down the trailer in 50mm increments. This enables the operator to ensure the axle loadings are exactly right and to also repurpose the trailer for other crane models enabling them to re-bolt on different furniture,” he said.
“Large fleet owners, like Freo Cranes might have trailers operating up in the Northern Territory as well as in Victoria. In the Northern Territory, they may want a road train configuration but in Victoria and especially with city driving in Melbourne for example, they may just want a straight semi-trailer. With VersaLock, the one trailer can be reconfigured and re-purposed to effectively go anywhere,” said Carden.
One of the models on display at the CICA Conference and Exhibition was a light weight, three-axle semi-trailer with the Versa-Lock mounting system. TRT has built the first two of these trailers for Universal Cranes.
“We also had a second trailer on display which could be classed as a crane support trailer. It’s an ESS trailer which incorporates our patented electronic steering system. We are currently building one for a NSW Crane company for their 500t Liebherr,” said Carden.
“The trailer is the first of its kind in Australia to do that job. The boom of the 500t crane will be taken off the crane and transported by this trailer. All 40 tyres on the trailer steer automatically with zero tyre scrub. They do this by way of a signal from the angle of the prime mover. This system will enable the whole boom, trailer and truck configuration in under what’s called 25m and provide them general access right around the city. It’s probably the only way they’d get their boom into the small lane ways of downtown Sydney,” he said.
“Almost everyone else operating this style of crane uses a quad float and a dolly, and when you use a dolly it’s not easy to back onto a site. This style of trailer will handle that.
According to Carden, it’s a new concept for transporting booms with flexibility engineered into the trailers. TRT has developed a new Quick Connect modular trailer system, which enables additional axle sections to be joined in 20 minutes or even less, without compromising strength. Something that could take an operator half a day or longer.
“We’ve got a number of them operating but not specifically to carry booms. In fact, one of the first to be delivered is to Max Cranes to carry the boom on their 1200t Liebherr, the largest all terrain crane in Australia. That trailer is unique in that it can be configured to carry the boom. But to increase flexibility, it can also have inserts taken out and axle modules added to make it an 8×8. Max Cranes can then put the whole 1200t carrier on it – which weighs 109 tonnes,” he said.
“It’s also possible to add ramps on the back and cart other bits of gear, or they could use the same trailer for transporting heavy loads like transformers. It becomes more than a trailer, it’s a piece of plant in their fleet that can be utilised in multiple applications. We started putting together this technology for Max Cranes about 12 months ago and the same technology from that build, is included in the NSW trailer.
TRT is always happy to discuss customer requirements, but these trailers are not off the shelf solutions, says Carden.
“Our Australian branch in Brisbane I supported by a team of 42, including a dedicated trailer sales team based there. Anyone interested in these trailers can contact Philip White and he’ll be able to provide advice and assist with developing a solution to suit specific applications. Philip has direct access to our factory and our engineers. Typically, with these things though they are not an off the shelf piece of kit, they require in-depth planning.
“We have a simple and effective process whereby we ask the customer what they want, find out what they need and then our engineering team works with our sales team and customers coming together with the optimal solution.
Along with our Warranty on workmanship, TRT Australia provides the service and support from Brisbane with a number of product support agents around Australia, depending on the trailer and what’s required,” he said.
If you would like to read the full article head on over to the the Cranes and Lifting website.