Top Mistakes Found During Routine Crane Inspections
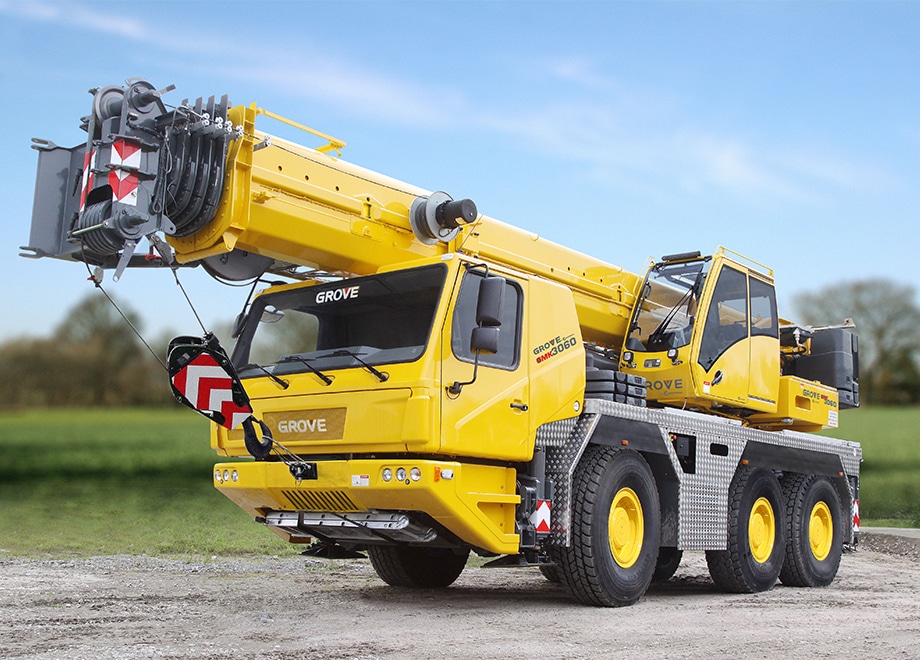
Why Routine Crane Inspections Matter in Australia
Routine crane inspections are a critical component of any safe worksite in Australia. With heavy lifting equipment operating under extreme loads and environmental stress, even a minor oversight during an inspection can result in serious consequences. These inspections are not just about ticking boxes—they are the frontline defence against mechanical failure, injury, and legal consequences.
Under Australian crane safety regulations and standards like AS 2550, employers and operators are required to conduct regular crane compliance checks to identify wear, damage, or malfunctioning components. But despite the existence of clear legal frameworks, many inspection processes fall short due to rushed routines, human error, or outdated systems. Even experienced teams make common crane inspection mistakes, often because they underestimate just how much can go wrong in what appears to be a ‘routine’ task.
Common Mistake #1: Skipping Pre-Use Checks
The Danger of Assuming Everything Works
One of the most frequent mistakes during routine crane inspections is skipping the pre-use checks. These inspections are designed to catch early signs of faults before the crane is put under load for the day. However, when operators are pressed for time, or the equipment looks fine on the surface, it becomes all too easy to assume everything is in working order.
How This Mistake Commonly Occurs on Busy Job Sites
On high-output worksites—particularly in construction and mining—operators often face pressure to begin tasks immediately. Shift changes, tight deadlines, and overlapping responsibilities lead to a culture where pre-use inspections are rushed or bypassed altogether. This false sense of routine reliability increases the chance of undetected wear, loose bolts, or hydraulic issues going unnoticed.
Real-World Example of Incidents Caused by Skipped Checks
In one well-documented incident from Western Australia, a tower crane’s slew ring failed mid-operation due to fatigue cracking that went unnoticed. Investigations revealed the fault would likely have been visible during a proper pre-use inspection. The repair costs were substantial, and the site faced a full shutdown pending a WorkSafe review—an expensive mistake stemming from complacency.
Common Mistake #2: Incomplete Documentation of Crane Inspections
Why Records Matter for Safety and Compliance
Accurate recordkeeping is a non-negotiable part of crane compliance checks in Australia. Not only does it serve as proof of diligence, but it also creates a maintenance trail that helps identify recurring faults. Under WHS laws and AS 2550, all routine crane inspections must be logged with clear notes on what was checked, who inspected it, and any remedial action taken.
Problems Caused by Handwritten, Inconsistent, or Missing Records
Many crane operators still rely on handwritten logbooks or spreadsheets stored on personal devices. This leads to inconsistent data, missing records, and difficulties tracing previous faults. If there’s a breakdown or incident, poorly documented inspections can leave companies open to liability, especially if regulators or insurers need to verify maintenance histories.
How to Digitise Inspection Records for Efficiency
Digital inspection tools allow crews to complete crane maintenance logs on mobile devices with checklists, photo attachments, and automatic date-stamping. This removes ambiguity, increases accountability, and ensures records are accessible across teams. Cloud-based solutions also make it easier to flag repeat issues and integrate data with wider asset management systems.
Common Mistake #3: Overlooking Structural Components
Cracks, Welds, and Rust—The Subtle Signs That Get Missed
Structural fatigue often begins as minor, almost invisible signs: small cracks in welds, rust around joints, or bent support plates. During routine crane inspections, these signs are sometimes missed, especially if inspectors lack training or tools to conduct close visual and non-visual assessments.
Parts Most Commonly Skipped in Routine Crane Inspections
Boom sections, turntables, slew rings, and counterweights are among the areas often overlooked. Structural issues in these parts can result in catastrophic failure if left unchecked, particularly under dynamic loads or in high-wind conditions.
Why Visual Inspections Alone May Not Be Enough
While visual checks are critical, they should be complemented with more advanced assessments like ultrasonic testing or magnetic particle inspection—especially for high-use cranes. Non-destructive testing (NDT) can identify internal fractures and flaws long before they become visible, enabling pre-emptive maintenance and reducing downtime.
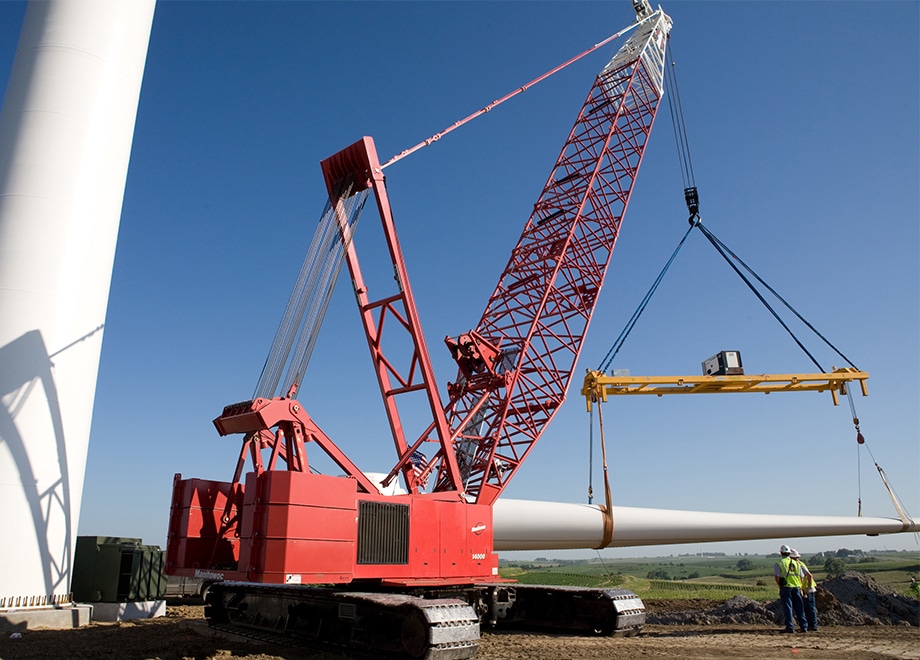
Common Mistake #4: Failing to Test Safety Systems
Limit Switches, Emergency Brakes, and Load Indicators
Crane safety systems are often the last line of defence in a mechanical failure. Yet, many routine crane inspections overlook fully testing these components. Limit switches, overload sensors, and emergency brakes can degrade over time or malfunction without obvious signs—until they are critically needed.
The Legal Risks of Operating with Faulty Crane Safety Features
Failing to test these safety systems is a major breach of Australian crane safety regulations. If a crane causes damage or injury and the investigation finds that emergency systems were faulty or untested, the consequences can include fines, license suspensions, or even criminal charges against responsible parties.
Simple Methods to Verify Proper Function
Incorporating specific test actions into the routine checklist—such as manually activating limit switches or load testing brake hold capacity—can prevent oversight. These tests take minimal time but play a huge role in ensuring crane safety systems perform as designed when it matters most.
Common Mistake #5: Rushing Through the Inspection Process
Why Time Pressure Leads to Oversights
Speed is the enemy of quality when it comes to routine crane inspections. Whether due to shift handovers, equipment availability pressures, or production targets, rushed inspections often lead to shallow assessments. This creates blind spots in safety checks and increases the risk of missing developing issues.
How Shift Changes and Deadlines Compromise Inspection Quality
When one team ends a shift and another begins, inspections are often assumed to be “already done” or repeated unnecessarily. Without clear handovers and documented signoffs, it’s easy for key components to be missed. In some cases, the same fault goes unnoticed by multiple teams because everyone thought someone else had already flagged it.
Establishing a Checklist-Driven Routine Crane Inspection Process
Structured checklists, with clearly defined responsibilities and timing, help eliminate these lapses. Every team should have access to standardised inspection protocols, and signoff procedures should be enforced to ensure compliance and continuity between shifts.
Training Team Members to Prioritise Thoroughness Over Speed
When crews are trained to understand the value of inspections, they’re more likely to take their time and follow procedures properly. Reinforcing this culture through toolbox talks and site audits helps create shared accountability and long-term improvements in crane maintenance outcomes.
How to Prevent These Crane Inspection Mistakes
Crane Inspection Checklists and Tools
Using comprehensive crane inspection checklists ensures that every inspection is consistent, thorough, and documented. Digital tools offer the ability to track inspection completion, flag missed items, and integrate photos or notes. These systems also help companies identify recurring faults or areas where further training may be required.
Apps and Software Designed for Crane Maintenance and Inspection Tracking
Modern crane inspection software includes GPS tagging, cloud backups, and maintenance reminders. Platforms like iAuditor or Papertrail allow companies to stay audit-ready and track crane performance over time, reducing the risk of crane inspection mistakes and making crane maintenance easier to manage.
Investing in Regular Staff Training
Keeping inspection staff up to date with Australian crane safety standards is vital. As equipment technology evolves, so do the inspection protocols. Offering refresher courses and engaging external auditors to review procedures helps keep your compliance levels high and your teams sharp.
What Happens If Routine Crane Inspections Are Done Poorly?
Poorly conducted routine crane inspections have led to serious incidents across Australian job sites. Collapsed booms, dropped loads, and control failures have all been traced back to missed maintenance or incomplete checks. These failures not only put lives at risk but can result in regulatory shutdowns, insurance claims being denied, and costly legal action.
Companies found in breach of their inspection obligations face fines that can run into six figures, as well as reputational damage that lingers long after the site reopens. Perhaps more importantly, the health and safety of workers is put in jeopardy when corners are cut on crane inspections.
Making Routine Crane Inspections Work for Your Site
Routine crane inspections are far more than a formality—they’re a strategic safety tool and a key part of responsible asset management. By avoiding these common crane inspection mistakes and embedding strong inspection protocols into daily operations, businesses can reduce downtime, prevent accidents, and stay on the right side of compliance laws.
Through training, the use of digital inspection systems, and a culture of thoroughness, Australian worksites can protect their teams and equipment alike. In the end, the cost of a proper routine crane inspection is always less than the cost of failure.